When you sink into your bed at the end of a long day, the comfort and support of your mattress might seem like magic. But behind that restful sleep lies a complex and fascinating process that brings the modern mattress to life. The journey from raw materials to the finished product involves creativity, precision, and a touch of science. So, what really goes on behind the scenes in the mattress-making world?
From Idea to Design
The mattress-making process begins long before any materials are cut or sewn. It starts with an idea—a vision of a product that meets the needs of specific sleepers. Whether it’s a mat designed for back pain relief or one that offers cooling properties for hot sleepers, the concept phase is where the journey begins.
Designers and engineers collaborate to create a blueprint for the mattress. They consider factors such as the target audience, sleep preferences, and the latest innovations in mattress technology. This stage is crucial because it sets the foundation for everything that follows. The design might even include options for custom bedding, where consumers can choose specific features like firmness levels or material types to suit their personal preferences.
The design process also involves extensive research and testing. Teams evaluate different materials, such as memory foam, latex, and innerspring coils, to determine which combination will provide the desired comfort and support. They also consider factors like durability, breathability, and environmental impact, ensuring the mat will not only feel good but also stand the test of time.
Selecting the Right Materials
Once the design is finalized, the next step is selecting the materials that will bring the mattress to life. The choice of materials is critical, as it directly affects the mattress’s performance, durability, and overall feel. Manufacturers source high-quality materials from trusted suppliers to ensure the final product meets strict quality standards.
For a memory foam mattress, polyurethane foam is the primary material. This foam is known for its ability to contour to the body, providing pressure relief and support where it’s needed most. Latex mattresses, whether made from natural or synthetic latex, offer a different feel—one that is more buoyant and responsive. Innerspring mattresses rely on steel coils for support, often combined with layers of foam or padding to enhance comfort.
The mattress cover is another essential component. Made from fabrics like cotton, polyester, or a blend, the cover not only protects the mattress but also adds to its comfort. Some covers are infused with cooling technologies or have antimicrobial properties, adding another layer of functionality to the mattress.
Prototyping and Refinement
With the materials selected, the next phase involves creating a prototype. This is where the design takes physical form, allowing the team to test and refine the mattress before it goes into full production. Prototyping is a hands-on process that requires attention to detail and a deep understanding of how each component contributes to the overall product.
During this phase, the prototype mattress undergoes rigorous testing to ensure it meets the design specifications. This might include pressure mapping to assess how well the mattress supports different body types, durability testing to simulate years of use, and thermal testing to evaluate temperature regulation. The feedback from these tests is invaluable, as it allows the team to make adjustments and improvements before mass production begins.
For example, if the prototype shows signs of premature wear or doesn’t provide adequate support in certain areas, the team might tweak the density of the foam or alter the arrangement of the coils. The goal is to create a mat that delivers on its promises of comfort, support, and durability.
The Manufacturing Process
Once the prototype is perfected, the mattress enters the manufacturing phase. This is where the design and materials come together in a carefully controlled process to create the final product. Manufacturing a mat involves several steps, each of which requires precision and expertise.
The first step is cutting the materials to the required dimensions. Large sheets of foam are sliced into layers, while coils are arranged into specific configurations for innerspring mattresses. Each layer is then assembled to form the core of the mattress. In the case of hybrid mats, which combine foam and coils, the layers are strategically stacked to maximize both comfort and support.
After the core is assembled, it’s time to encase it in the mattress cover. The cover is sewn together and then fitted over the mattress, creating a smooth and finished appearance. Some mattresses also include additional features, such as reinforced edges for added durability or handles to make moving the mattress easier.
Quality control is an integral part of the manufacturing process. Each mat is inspected to ensure it meets the required standards for size, shape, and performance. Any defects are identified and corrected before the mattress is packaged for shipment. This step is crucial in maintaining the high standards that consumers expect from their mats.
Sustainability in Mattress Production
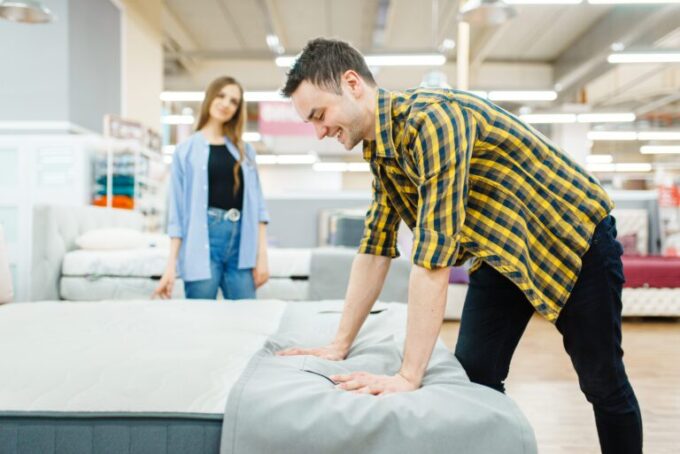
Source: liquid-features.com
In today’s world, sustainability is a key consideration in mat manufacturing. As consumers become more environmentally conscious, manufacturers are taking steps to reduce their impact on the planet. This includes using eco-friendly materials, such as organic cotton, natural latex, and recycled fibers, as well as adopting more sustainable production methods.
For example, some manufacturers are moving towards zero-waste production, where all materials are used efficiently, and any scraps are recycled. Others are exploring alternative materials, such as plant-based foams or biodegradable fabrics, to reduce the use of petroleum-based products. These efforts not only help protect the environment but also appeal to consumers who value sustainability in the products they purchase.
Sustainability also extends to the durability of the mat. A well-made mat that lasts for years is more environmentally friendly than one that needs to be replaced frequently. By focusing on quality and longevity, manufacturers can reduce waste and offer consumers a better return on their investment.
From Factory to Your Bedroom
After the mattress is manufactured and passes all quality checks, it’s time for it to make its way to your bedroom. This stage of the process has seen significant innovation in recent years, particularly with the rise of the “mattress in a box” concept. This method involves compressing and rolling the mat into a compact box for easy shipping, making it more convenient for consumers to receive and set up their new mat.