Are you worried about CNC machining performance when working with magnesium, a notoriously challenging material? Magnesium is a versatile and lightweight metal commonly used in various industries, including aerospace, automotive, and electronics.
However, magnesium CNC machining can be challenging due to its flammability and unique properties. To maximize CNC performance in magnesium machining, it’s crucial to employ specific techniques and precautions. In this article, we will delve into five essential strategies for achieving the best results in magnesium machining.
Avoid Tight Relief Angle
In magnesium machining, the choice of tool geometry and relief angles is paramount. Magnesium’s low thermal conductivity makes it prone to heat buildup during cutting, which can lead to accelerated tool wear and reduced machining performance. To mitigate these issues, it is essential to select cutting tools with generous relief angles for CNC Machining.
In magnesium machining, tight relief angles should be scrupulously avoided. These angles refer to the clearance or angle on the cutting tool’s edge, which directly influences the interaction between the tool and the workpiece. A tight relief angle can lead to increased friction and heat generation during the machining process. This elevated heat can result in premature tool wear and, consequently, a reduced tool lifespan. Additionally, it can negatively impact surface finishes, compromising the overall quality of the machined part.
To mitigate these issues and enhance the CNC machine Shop’s performance in magnesium machining, it is advisable to opt for larger relief angles. These more generous relief angles serve several crucial purposes. Firstly, they promote efficient chip evacuation, preventing chips from becoming trapped between the tool and the workpiece, which can lead to tool jamming and decreased machining efficiency.
Secondly, larger relief angles aid in reducing heat buildup by providing a smoother surface for chip flow. This helps maintain stable cutting temperatures, which are vital for both tool longevity and the prevention of undesirable material behaviors such as ignition or welding.
Make Discontinuous Chips
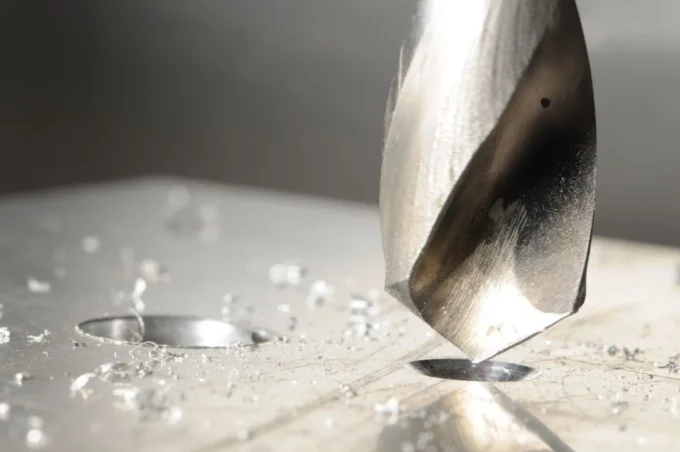
Source: dizz.com
In the process of magnesium CNC machining, the generation of chips can either streamline the process or become a significant hindrance. Unlike other materials, magnesium exhibits a proclivity for producing long, stringy chips when machined conventionally. These elongated chips pose multiple challenges.
Firstly, they increase the risk of tool jamming and premature wear. Secondly, they can obstruct the machining area, necessitating frequent pauses for chip removal, thereby reducing machining efficiency.
To overcome these issues and maximize the CNC Machining of magnesium, it’s imperative to adopt techniques that encourage the formation of discontinuous chips. Discontinuous chips are characterized by their shorter length and reduced tendency to tangle or wrap around the cutting tool. Achieving this desired chip morphology requires a strategic approach.
One effective strategy is to adjust the machining parameters, primarily the feed rate and cutting speed. By increasing the feed rate and lowering the cutting speed within safe limits, you can promote the creation of shorter, segmented chips. This adjustment optimizes the chip-breaking process, ensuring that chips are more manageable and less likely to cause disruptions during machining. Additionally, it enhances tool life as the cutting tool encounters less stress and wear.
Use an Explosion-proof Vacuum for the Chips
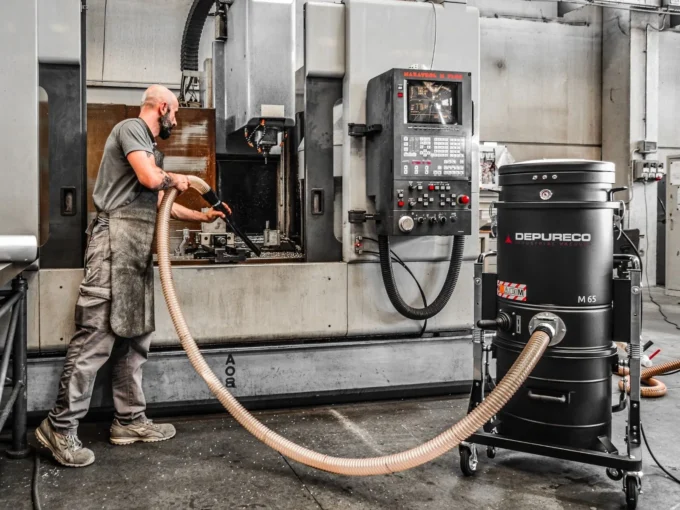
Source: depureco.com
Handling magnesium chips demands a comprehensive safety approach. Magnesium’s extreme flammability makes it imperative to employ specialized equipment to manage the chips safely. An explosion-proof vacuum system is a pivotal component of this safety protocol. Unlike conventional vacuums, explosion-proof units are designed with robust construction and specialized components that minimize the risk of sparking, which could ignite magnesium chips.
These vacuums are equipped with features such as grounded hoses, static-conductive materials, and spark-proof motors, all meticulously engineered to prevent any potential ignition sources. Moreover, explosion-proof vacuums often incorporate HEPA filtration systems to ensure that fine magnesium particles are effectively captured, reducing the risk of airborne hazards.
When it comes to disposing of collected magnesium chips, it’s essential to follow proper procedures. The collected chips should be stored in designated fire-resistant containers or bins specifically designed for magnesium. These containers should be located in a safe area, away from potential ignition sources, until the chips can be safely disposed of in accordance with local regulations.
Incorporating an explosion-proof vacuum system into your CNC Machining setup not only enhances safety but also improves overall efficiency. It enables you to maintain a clean workspace, reduces the risk of magnesium-related fires, and ensures compliance with safety regulations. By investing in this critical safety measure, you can confidently harness the advantages of magnesium as a machining material while mitigating the inherent risks associated with its use.
Use Mineral Oil Coolants
Effective cooling is paramount in magnesium machining to prevent the material from reaching critical temperatures that can lead to ignition and prolong the lifespan of cutting tools. The choice of coolant plays a significant role in achieving these goals. Mineral oil-based coolants are a preferred option for machining magnesium due to their unique properties that enhance both cooling and lubrication.
Mineral oil coolants offer several advantages when working with magnesium. Firstly, they have excellent heat-absorbing properties, efficiently dissipating the heat generated during the machining process. This is critical as magnesium has a low melting point and can easily ignite when exposed to high temperatures. By maintaining stable cutting temperatures, mineral oil coolants help prevent the risk of ignition, ensuring a safer machining environment.
Secondly, mineral oil coolants provide effective lubrication, reducing friction between the cutting tool and the workpiece. Reduced friction translates to less tool wear, longer tool life, and improved surface finish. Moreover, the lubricating properties of these coolants enhance chip evacuation by reducing adhesion, which is especially crucial in magnesium machining, where long, stringy chips are common.
Furthermore, mineral oil-based coolants are chemically stable when exposed to magnesium, minimizing the risk of undesirable reactions that can occur with some other types of coolants. This stability ensures that the coolant remains effective throughout the machining process, contributing to consistent performance and reduced downtime for coolant changes. It’s essential to select the appropriate concentration of mineral oil coolant to achieve the desired cooling and lubrication effects. CNC machine Shops should closely follow manufacturer recommendations and regularly monitor the coolant concentration to maintain optimal performance.
Never Use Water to Extinguish Magnesium Fire
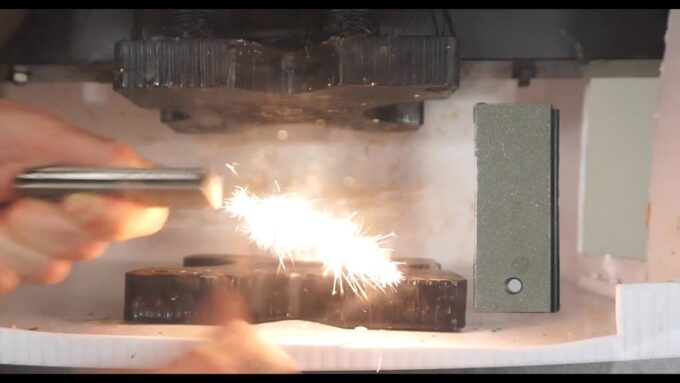
Source: m.youtube.com
Water and magnesium are a perilous combination when it comes to fire management. Magnesium has a remarkable affinity for oxygen, and when it burns, it releases an intense heat that can reach temperatures of up to 5,600°F (3,100°C). When water is applied to a magnesium fire, it reacts vigorously, producing hydrogen gas. The hydrogen gas not only feeds the fire but can also lead to explosive consequences, endangering both equipment and personnel.
To tackle a magnesium fire safely, it is imperative to utilize a Class D fire extinguisher designed explicitly for metal fires or a dry sand extinguishing agent. These methods work by smothering the fire, cutting off its oxygen supply, and effectively suppressing the flames without exacerbating the situation. Always have these specialized fire suppression tools readily available in any workspace where magnesium machining occurs to ensure the utmost safety during machining operations.
Conclusion
when it comes to mastering the art of magnesium machining, remember that precision and safety go hand in hand. By embracing these cutting-edge strategies, you’ll be forging a path toward CNC Machining excellence, where every cut counts. So, gear up, employ these techniques, and watch your CNC machine shop performance soar to new heights, all while keeping those fiery challenges at bay.