If you run a business in which you have a lot of waste heat as a byproduct of your operations, you are probably using cooling towers. Cooling towers are devices made for heat rejection. They reject excess heat through the use of water steam and lower the temperature of the whole production process. The better their performance the more a factory, a refinery, or a plant can produce. There are a few different models of cooling towers but one thing is true for all of them. They are key components in the overall system that makes the operation run smoothly because if they are not operating to the most of their capabilities, nothing else can. There is simply too much heat for other parts of the production process to function and everything shuts down.
In order for your cooling tower to work properly, you have to know all there is to know about them. What is more, maintaining their operation and improving their performance should be at the very top of your list of things to pay attention to. If you need help and some advice about this, you have come to the right place. In the article before you we will discuss the best ways to improve your cooling tower performance. Make sure to navigate through the following sections carefully so as not to miss a crucial piece of advice that can help you down the line.
About Cooling Towers
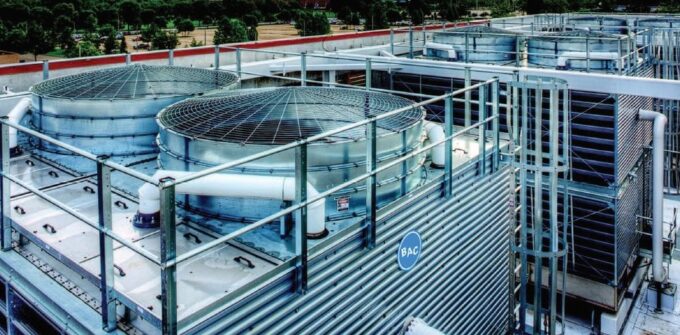
Source: westmechinc.com
Before we can talk about how you can improve their performance, we should mention a thing or two about the towers themselves. They vary in size greatly and they range from small rooftop containers or barrel-size devices to monstrous structures you have probably seen around your city. Reaching up to 200 meters in height and 100 meters in diameter, they are usually circular. Rectangular types exist as well but they are often smaller. Coal and nuclear power plants use them the most, but basically any kind of refinery, factory, or plant that deals with excess heat has them. Air conditioning heat can also be dealt with through these devices and many small units can exist near or on the buildings that need cooling.
The first towers started appearing in the 19th century following the creation of steam engines and condensers. The first modern, hyperboloid tower appeared in 1918 and since then they took over the Netherlands, the United Kingdom, and other industry-rich 20th century countries. Nowadays, it is impossible to imagine the industry without HVAC (heating, ventilating, air conditioning) cooling towers there to reject all the unwanted heat from the processes of production. This is why you should take care of your own and aim to upgrade it as much and frequent as possible.
Ways to Improve the Towers
Now would be time to move onto the more concrete information regarding the proper maintenance and improvement of the cooling towers you may have in your business. Remember, whatever size they are and however busy they may be, they are crucial to whatever it is they are cooling down. Therefore, make sure to adopt as many of the following tactics and approaches as possible in your situation.
1. Change Old and Broken Parts
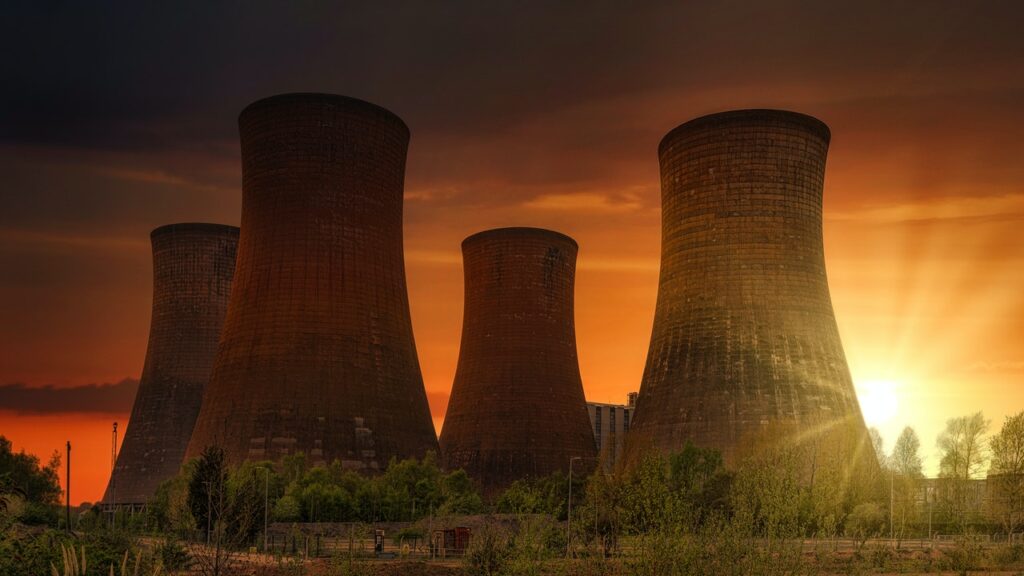
Source: pexels.com
Changing the parts that have been in operation for years in favor of fresh and new ones is the best way to ensure a prolonged life of any type of machinery no matter how simple. Cooling towers have so many moving and important elements that are prone to damage and wear and tear over time. You simply have to think about them often in order to prevent downtime. Downtime leads to revenue loss and that is what you must prevent at all costs. Parts of the water cooling tower that may need frequent change include fan stacks, fans, gearboxes, motors, fill media, nozzles, drive shafts, assemblies, FRP members, drift eliminators, and hardware. If you want to know more about the as well as where to get them form, make sure to check out Industrial Cooling Solutions.
2. Inspections
In order to know if parts need changing or not, you have to have a closer look at them. This of course comes in the form of careful inspections by professionals who are educated in the ways cooling towers should be maintained and upgraded. Every once in a while, have an inspection team do their thing to prevent the usual ways in which they can become damaged. You will also eliminate the need for more frequent changing of parts if you inspect your towers as much as you should. Regular inspection of all equipment is crucial, not just the cooling parts.
3. Increase of Cycles
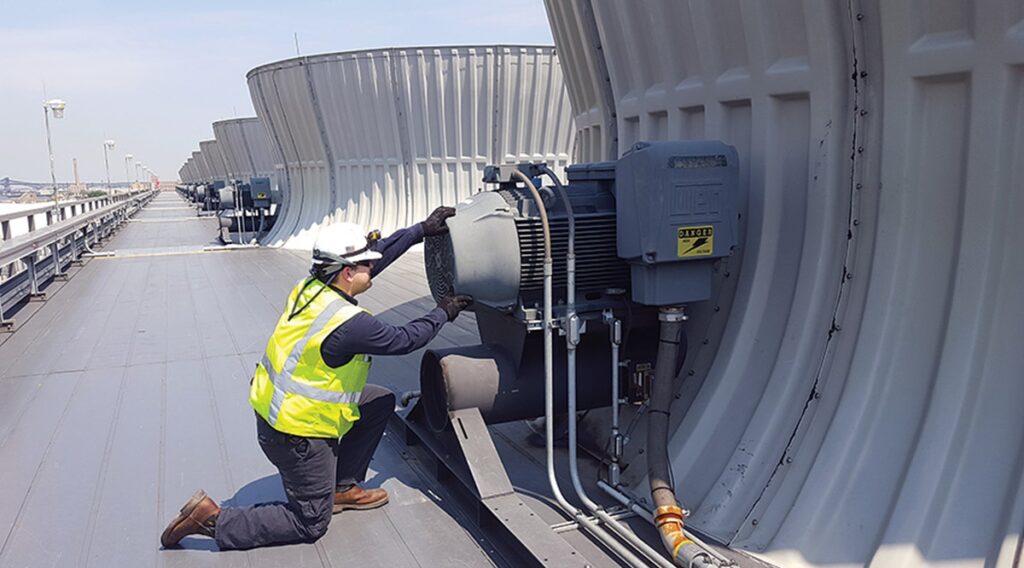
Source: thehackpost.com
The number of cycles the cooling tower uses is the most important thing to know about it. Being aware of it can help you increase its performance which will directly lead to more of your products being made. If you manage to up the cycles, you could reduce make-up water by as much as 20%, as well as reduce the blowdown by up to 50%. Focusing on the towers is not something most employees and employers focus on simply because it does not seem as a priority. They view is as a necessity and nothing else, when in fact it can read directly to a higher volume of production. Improving the efficiency of the water you are using will also preserve energy, save you money, allow a smoother operation process, and give you a chance to improve in other areas too.
4. Recycling
As mentioned, saving energy and reusing what you can is among the best ways to increase production and save costs. For better water management and energy preservation, recycling at least 98% of your water should be your number one goal. The best towers on the market are made to recycle as much, so if you want your performance to be at a higher level you should aim at being as close to that number as possible. You will not believe how much you are saving if you go out of your way to reuse water.