Electrical cables are a part of every device we are using, and they are the reason why power can flow from the outlet to the device. There are many different types of these products, and most people don’t know what these consist of. If you want to know more about them, you’ve come to the right place. In this 2024 guide, we will tell you how an electrical cable is made, and we will give you more information on all the parts that you can find in one.
Parts of the cable
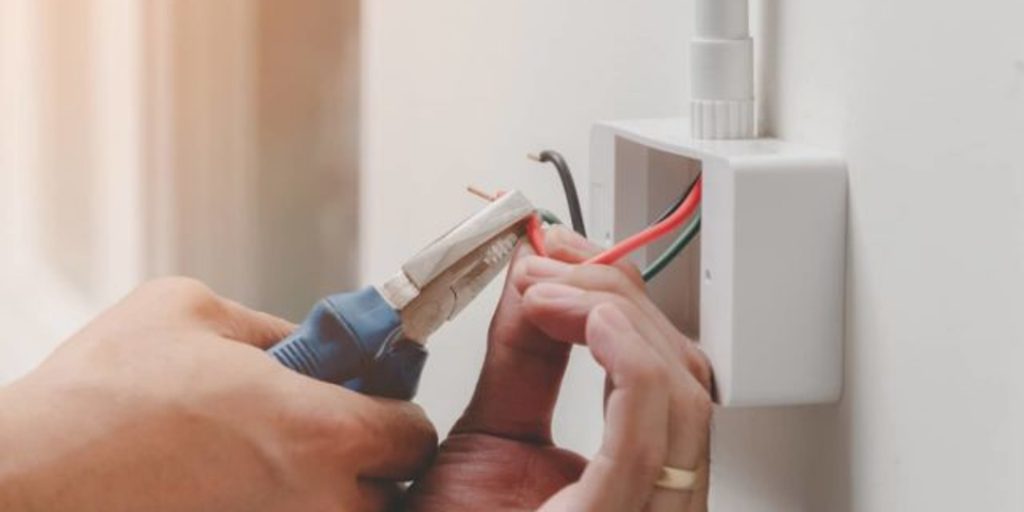
Source: mistersparky.com
Let’s start by giving you more information on what the cable consists of. There are four main parts that you can find in these, and they include the conductor, the insulation that goes around the wires, metal protection, and the outer sheath.
The most common material used to create the conductor is copper, as it is the one that transmits electricity the best, and it is also one of the cheapest materials that you can use. In some cases, aluminum can be implemented. When it comes to copper, there are two main sizes that manufacturers use, and the thickness depends on the task at hand, and how the cable will be used.
The reason why manufacturers steer away from aluminum is that compared to copper, it transmits electricity almost 70 percent worse. The only industry in which aluminum is preferred is in the power cables that electrical companies use.
Now that you know more about the conductor, let’s talk about the protection that goes around the wires and keeps them together. The insulation usually consists of plastic or polymer, and once again, depends on the type of material used for the conductor.
The reason why we need insulation around the wires is to protect them from external conditions, as well as protect the environment from the wires. As you already know, the wires can get hot, and if there isn’t anything to keep that temperature steady, it could easily lead to a fire.
Note that the materials used for this process will stay intact even if the temperature gets as high as 160 degrees Fahrenheit. However, there are materials that will protect it even if the temperature gets to 200 degrees Fahrenheit or 90 degrees Celsius.
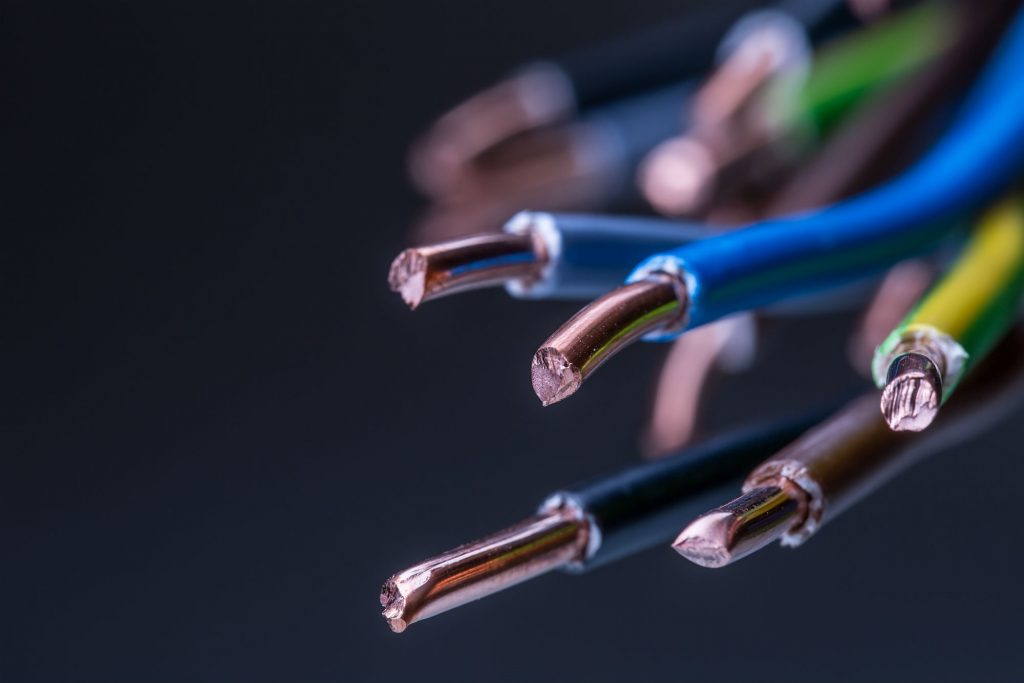
Source: electroniccentre.ca
There are two main ways to create the insulation part – thermoplastic and thermosetting. The former is easier to create, and it protects the cable from lower temperatures, where the latter is considered heavy-duty protection, and it is utilized for equipment that needs to transmit a lot of power and stay intact.
As you can see on websites like zwcables.com, even though there are different types of electrical cables, they are made of the same parts, and the manufacturing process depends on the purpose.
The metal protection is the next part of the cable, and they do two types of protection – it isolates the signals, and they protect it from outside interference. The screens that are used are mostly made to help the power easily go through the cable, no matter the conditions, whereas the armors or the materials that are made to physically protect lines are there to help prevent any type of possible damage.
So, the protectors are there in case the cable gets wet, or if someone runs over it, or even if it falls from great heights. Even though there are some things that will physically damage the cable, this part prevents more than 80 percent of the damages that would occur if it was not wrapped with it.
The last part that is used in the making of these is the outer sheath. Some products do have this part, while others don’t. Manufacturers choose if they are going to implement it or not depending on the type of wires used, the purposes of the cable, as well as the conditions where it will be placed. This is another part that is made to protect it, and it gives additional coverage. Even though the cable could perfectly work on its own just with the metal protection, the sheath adds an additional layer of coverage. It helps prevent outside damages and helps in keeping it intact even if it has to be put and used at heights, or if it is buried in the ground.
How are they made?
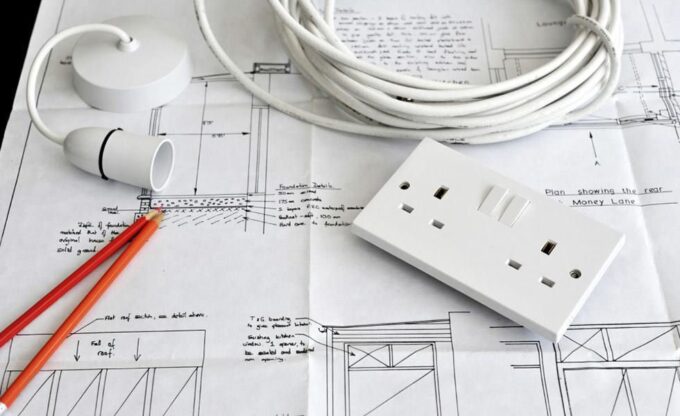
Source: homebuilding.co.uk
There are many steps into this process, and if you want to know each of the smaller steps, then the best thing you can do is talk to a manufacturer that can not only tell you more about it but they can also show you how they are made.
The first thing that is done is the extraction process, and metal is taken out of the ore. There are several ways to do this, and mining is involved. After that, a special machine is used to create the copper wires that we talked about before.
During the assembly process, several machines are utilized, and they all work on creating wires that are going to be of the same size and the same length. After that, the inner coverings are made, and they are wrapped around the wires.
For the next step, the armor is created, and once again, the wires are layered with it. Once everything is made, and once everything is put together, the cable needs to be inspected. It goes through quality assessment, and every part is checked. In case there are any issues, or if there are any breakages or damages, it does not go through the next step.
Once it passes the check, the cable is then cut into the needed length, and the final parts are added. The quality of the cable can be measured in different lengths, and the manufacturer needs to have all the proper certifications and machines to be able to produce these.
That’s it! This is how an electrical cable is made, and it is actually easier done than explained. There are more than 20 different types of cables that you can find on today’s market, and even though they have different purposes, they are all made in a really similar way, using similar machines and technology.