Selecting the appropriate equipment for your food business is crucial to ensure efficiency, quality, and safety. One of the most critical pieces of equipment for food preservation and packaging is the PSA nitrogen generator.
This technology is instrumental in maintaining the freshness and integrity of various food products, making it a valuable asset for any food business.
Incorporating a nitrogen generator for the food industry can significantly enhance the shelf life of products, improve package integrity, and ensure a high level of product quality. This article will guide you through the essential factors to consider when choosing the right PSA nitrogen generator for your food business.
Understanding PSA
-
What is PSA Technology?
Pressure Swing Adsorption (PSA) technology is a widely used method for generating high-purity nitrogen. This technology separates nitrogen from the air using adsorbent materials, typically carbon molecular sieves, which adsorb oxygen and other impurities. The result is a continuous supply of pure nitrogen, essential for food packaging and preservation.
-
Benefits of PSA
PSA offers numerous advantages, including on-site production, cost savings, and consistent purity. These benefits make PSA generators an ideal choice for food businesses looking to enhance their packaging processes and product quality.
Key Considerations for Choosing
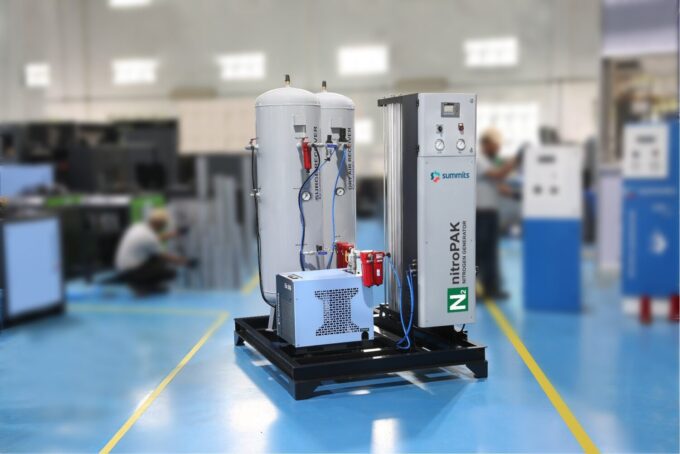
Source: m.indiamart.com
-
Purity Requirements
Different food products have varying purity requirements. For instance, high-purity is crucial for packaging delicate products like dairy and bakery items. Determine the specific purity needs of your products to select a generator that meets these requirements.
-
Production Capacity
The production capacity of a PSA nitrogen generator should align with the volume of nitrogen required for your food business. Assess your production demands and choose a generator that can consistently supply the necessary amount of nitrogen without interruptions.
-
Operational Costs
Consider the operational costs associated with running a PSA nitrogen generator. These costs include energy consumption, maintenance, and potential downtime. Opt for a generator that offers energy efficiency and low maintenance requirements to minimize operational expenses.
-
Space and Installation
Evaluate the available space in your facility for installing PSA. Some generators have a compact design suitable for smaller spaces, while others may require more extensive installation areas. Ensure that the chosen generator fits seamlessly into your existing setup.
-
Maintenance and Support
Regular maintenance is essential to ensure the longevity and efficiency of PSA. Choose a generator from a reputable supplier that offers comprehensive maintenance and support services. This will help in maintaining optimal performance and minimizing downtime.
Applications in the Food Industry
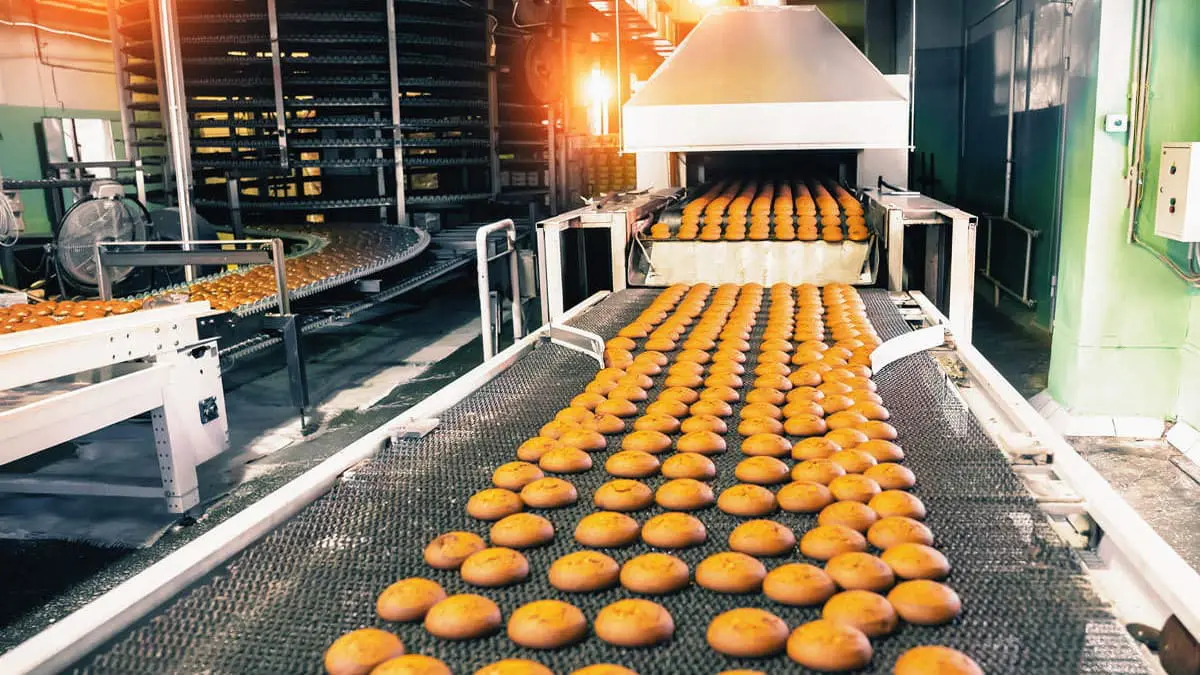
Source: tecnosida.com
-
Fresh Produce Packaging
PSA nitrogen generators are extensively used in packaging fresh produce. The atmosphere created by the generator helps in preserving the freshness and appearance of fruits and vegetables by slowing down the ripening process and reducing spoilage.
-
Meat and Poultry Packaging
In the meat and poultry industry, maintaining product quality is paramount. Nitrogen generators provide an oxygen-free environment, which inhibits the growth of bacteria and extends the shelf life of these products. This ensures that the meat and poultry reach consumers in the best possible condition.
-
Dairy Product Packaging
Dairy products are highly perishable and require careful packaging to maintain their quality. PSA nitrogen generators help in creating an inert atmosphere within the packaging, preventing spoilage and maintaining the freshness of dairy items like cheese, milk, and yogurt.
-
Bakery Product Packaging
Bakery products, especially those without preservatives, benefit greatly from nitrogen packaging. The nitrogen environment prevents mold growth and retains the softness and taste of baked goods. This is crucial for ensuring that bakery products remain fresh until they are consumed.
Evaluating Features
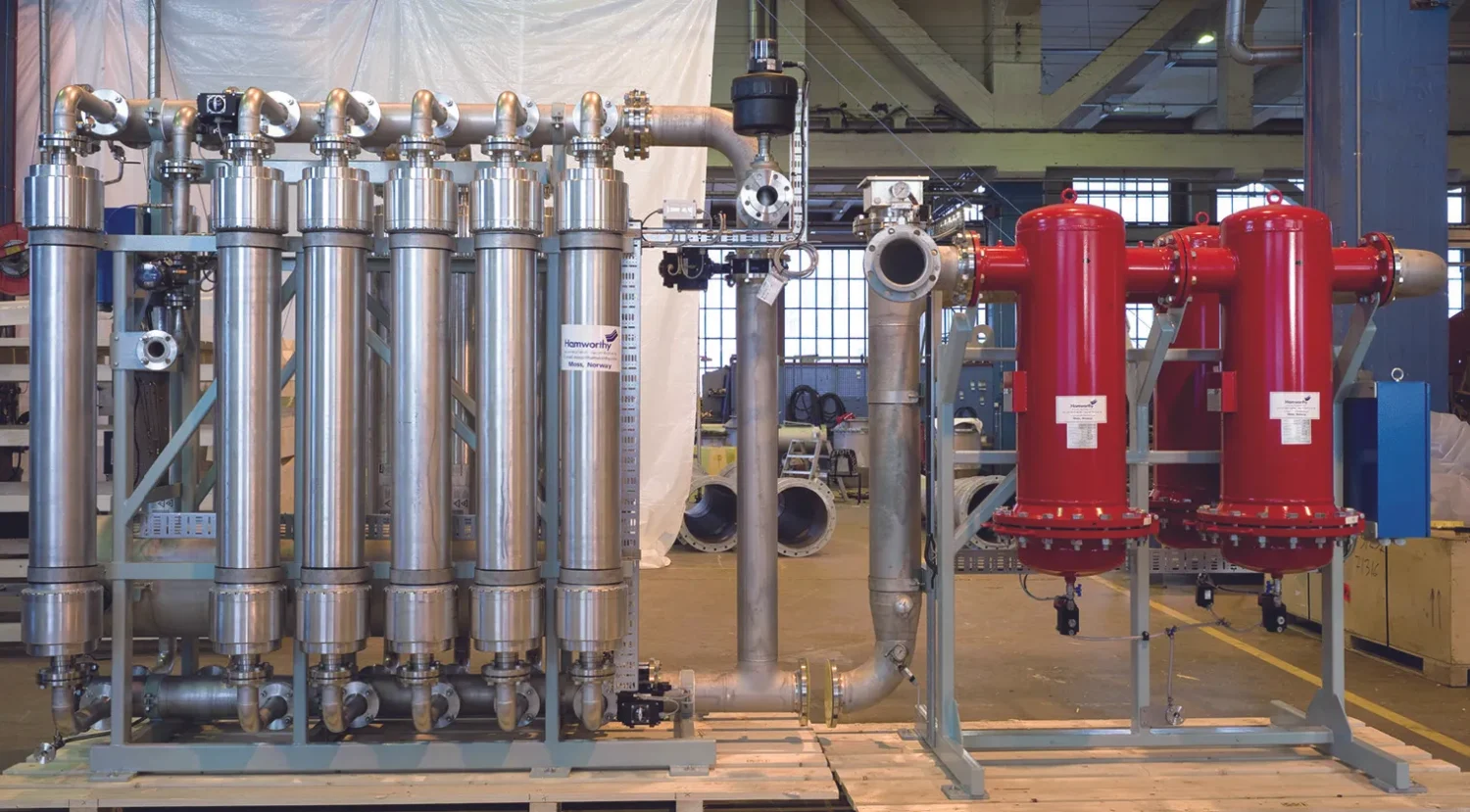
Source: wartsila.com
-
Automation and Control
Modern PSA nitrogen generators come equipped with advanced automation and control systems. These features allow for precise control of nitrogen flow and purity levels, ensuring consistent quality in food packaging operations. Look for generators with user-friendly interfaces and automated controls for ease of operation.
-
Energy Efficiency
Energy efficiency is a critical factor when selecting a PSA nitrogen generator. Generators with energy-saving features can significantly reduce operational costs. Evaluate the energy consumption of different models and choose one that offers optimal performance with minimal energy usage.
-
Durability and Reliability
Investing in a durable and reliable PSA nitrogen generator is essential for long-term success. Look for generators constructed from high-quality materials and with a proven track record of performance. Reliable generators reduce the risk of downtime and ensure continuous nitrogen supply.
-
Customization Options
Some PSA nitrogen generators offer customization options to meet specific business needs. Whether it’s adjusting nitrogen purity levels or integrating with existing systems, customization can enhance the efficiency of your packaging process. Choose a generator that allows for tailored solutions to suit your unique requirements.
Case Studies: Successful Implementations
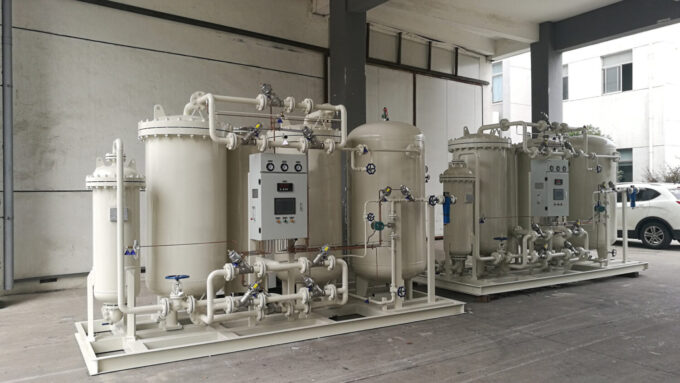
Source: honproducts.com
-
Fresh Produce Distributor
A fresh produce distributor implemented a PSA nitrogen generator to extend the shelf life of their products. By maintaining a nitrogen-rich atmosphere in their packaging, they significantly reduced spoilage rates and enhanced the visual appeal of their fruits and vegetables. This led to increased customer satisfaction and reduced waste.
-
Meat Processing Plant
A meat processing plant faced challenges in preserving the quality of their products during storage and transportation. By integrating a PSA nitrogen generator, they created an oxygen-free environment that inhibited bacterial growth. This resulted in extended shelf life and improved product quality, leading to higher sales and customer trust.
-
Dairy Manufacturer
A dairy manufacturer needed a solution to maintain the freshness of their products without relying on preservatives. By using a PSA nitrogen generator, they created an inert packaging environment that preserved the taste and texture of their dairy items. This allowed them to offer preservative-free products with an extended shelf life, appealing to health-conscious consumers.
Future Trends and Innovations
-
Integration with Smart Packaging
The future of PSA nitrogen generators lies in their integration with smart packaging technologies. Smart packaging, equipped with sensors and IoT devices, can monitor the internal environment of the package in real-time. By combining this with PSA nitrogen generators, manufacturers can achieve even greater control over product quality and shelf life.
-
Advances in Generator Technology
Ongoing advancements in PSA nitrogen generator technology are expected to enhance their efficiency and performance. Innovations such as energy-efficient designs and improved automation systems will make these generators even more cost-effective and environmentally friendly.
-
Sustainable Packaging Solutions
The demand for sustainable packaging solutions is on the rise. PSA nitrogen generators, with their ability to extend shelf life and reduce waste, will play a crucial role in meeting this demand. Manufacturers are likely to explore new ways to integrate these generators into eco-friendly packaging materials and designs.
Conclusion
Choosing the right PSA nitrogen generator for your food business is a strategic decision that can significantly impact product quality, shelf life, and operational efficiency. By understanding the specific needs of your business and evaluating key factors such as nitrogen purity, production capacity, and operational costs, you can select a generator that meets your requirements and enhances your packaging processes.