A mirror is glass, so is your jar, but aren’t they both different? Do you find the tinted window glass the same as that of your teacup? Glass is one of the versatile materials used in every domain, having as many variations as its applications.
We all have glass bottles for stocking kitchen supplies, collecting coins, storing chemicals in labs, or growing plants. If you have ever wondered how are glass bottles made, here’s a detailed guide to walk you through all the steps and procedures.
Glass varieties chosen for manufacturing bottles
Glass is initially a liquid product heated at 1700 degrees Celsius and then cooled down, resulting in a solid mass. For containers and bottles, industries alter the commercially manufactured glass in its cooling temperatures and properties.
Purity of the Glass used
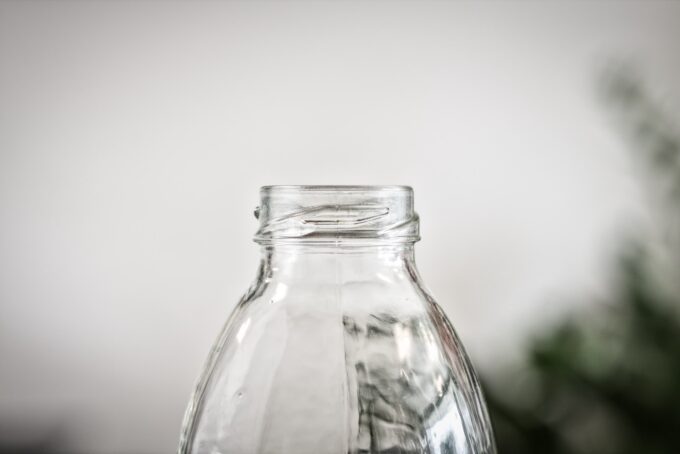
Source: unsplash.com
The glass is a mixture of silicon dioxide, sodium carbonate, calcium carbonate, and cullet. Cullet is recycled glass powder that manufacturers add to reduce the energy and time consumed in the production.
The more is the cullet’s ratio, the lesser the other raw materials and energy are required as the glass quickly melts into liquid gobs. For jars, cullet can be in the range of 25% to 60%, which alters their strength and durability.
Added property enhancers
Glass for jars differs in thickness, heat resistance, color, and flexibility to shape. Higher silica content from silica sand or quartz provides more variations in bottles’ colors. Adding oxides of aluminum and magnesium increases durability. Limestone generates calcium oxide, which enhances the resistive properties of the glass.
Commercially, manufacturers add sodium or soda to reduce the melting temperature to control the energy required for the production. Additionally, elements like boron, sulfate, or magnesium are common to use for producing tinted shades.
Varieties of Glass
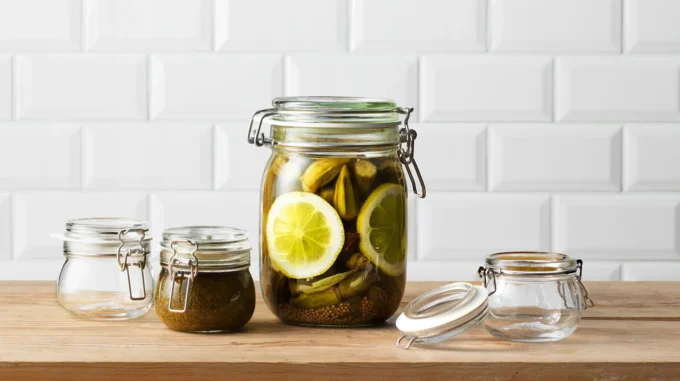
Source: ikea.com
Jars and bottles usually use three types of glass- borosilicate, treated soda-lime, and soda-lime-silica. All the varieties contain substantial alkali metal oxides, which improve chemical durability to resist water and enhance thermal expansion.
Borosilicates are the toughest of all and are generally used for laboratory jars and chemical storage containers. The kitchen jars are made of soda-lime containing lower magnesium and aluminum to increase chemical resistance.
Steps for manufacturing glass jars and bottles
Making bottles of varied shapes and colors requires a few more steps in comparison to the flat glass produced for window panes and mirrors. This manufacturing has to consider various sizes, dimensions, and colors according to the designs in demand. The following steps discuss the general stages of how a glass bottle from roetell.com is made industrially.
Preparing molds
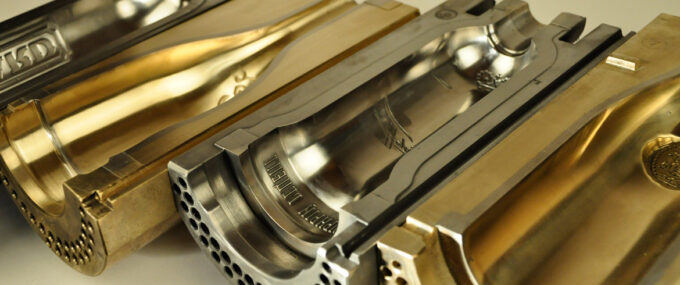
Source: glass-container-mould.com
The manufacturing procedure is completely automated using machines working under high pressure and temperature. The first step is designing the appropriate mould to define the shape and dimensions of the bottle. The molds are generally made of stainless steel to withstand the blazing temperature of liquid Glass.
Manufacturing raw Glass
Raw materials as discussed are purified, powdered, and collected in the furnace to heat and melt together. Enhancers and cullet are also added at this stage. The furnaces are closed and protected structures like industrial hoopers with a constant fire supply. Industries use cranes and lifters to deposit the materials into external valves of the hot furnace tunnel. The furnace constantly heats this mix till a uniform and dense mass of amber color forms.
Refining the raw mixture

Source: truelegacyhomes.com
Liquid glass is then refined to remove the dust and air impurities, finally giving out a honey-looking substance further cut into gobs. High precision machinery working on pre-decided time intervals cut the dropping liquid glass into chunks of equal weight.
These small masses of molten raw glass are the gobs. Since the molds designed in the first stage produce bottles of similar dimensions, the automatic cutter divides gobs into equal masses.
Molding into bottles
These small chunks are now sent to the molds for forming the precise bottle shape. Forming is a two-step process where the primary structure is given with basic dimensions. This stage is called a parison, which is the basic design.
In the next step, the air is blown into it to completely set the liquid inside the mold to give out the final shape. There are two different industrial procedures used for finalizing dimensions. It depends on whether the neck has a uniform thickness or has varied fancy thicknesses.
Inspection for inconsistencies
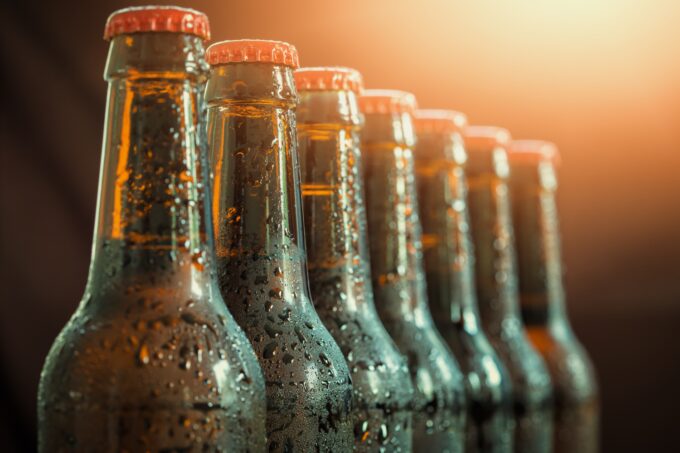
Source: truelegacyhomes.com
The shaped glass bottles are still hot as they are released from the molds for visual inspection. Cracks, impurities, air bubbles, or inconsistent thickness are measured and examined at this stage to finalize the product.
Cooling down using annealing lehr
The final bottles are somewhere around 600 degrees Celsius, subsequently cooled to a suitable temperature of 60 degrees. Lehr is the cooling kiln used, and annealing is the term for the process. Cooling eliminates the internal stress to strengthen the bottles. Finally, after keen inspection the industry ensures the marketing standards and packs the bottles in required batches.
Different molding methods and their effects
After obtaining the liquid glass parison (the primary form of the mold), manufacturers can opt for different heating and forming procedures to give out variations in size and thickness. They use automatic IS or Individual Section machines having several slots to produce multiple bottles at a time.
The press-and-blow process reheats the basic mold, transfers it to a blowing mold of defined dimensions, and flushes it with air to create wide-necked bottles. The blow-and-blow method uses compressed air to flush inside the parison in the same mold to make thin-necked bottles. The former process forms a parison using gravitational fall into the mold, whereas the latter creates an inverted parison and molds it using compressed air.
Conclusion
Glass produced under different conditions implies different properties. Jars and bottles can be colored or transparent, thick or thin-walled, or fragile or dense. Depending on the purpose of bottles and the glass quality used in their make, you should choose the appropriate type and brand.
Several times, you can find jar and bottle manufacturing companies guiding for the temperature and chemical resistivity of the bottles to choose the apt. Glass is comparatively eco-friendly over plastics as it uses recycled cullet in the manufacturing process to reduce the energy consumed in production.