If you’re working on a new machine that features an electromechanical system, one of the most important things that you could ensure is that you obtain the positional feedback from all the components that move. This means that you’ll need to have control of the machine’s motion, something that you can do with the help of an encoder.
But, once you do some digging online, you’ll find a wide range of encoder solutions, which is why you might be wondering – how can I find a suitable option for my project? Luckily for all people that are wondering the same thing, the article below can help. Let’s take a closer look at what you should know and consider:
Learn If You Really Need it
The first thing that you should know is that these machines will close feedback loops, which means that they’ll tell you what the moving components are doing. But, some of the systems operate on open loops, hence, you might need a different mechanism instead of an encoder. Depending on what you’re working on, you could choose to use a stepper motor, commutation, or a simple switch.
Keep in mind, if you truly want to see accurate positioning information, if you want to learn how fast something is moving & in which direction, as well as the distance covered, you’ll need to purchase an encoder. If so, the next thing you should do is to consider how you’ll use it.
Consider The Conditions Around The Device
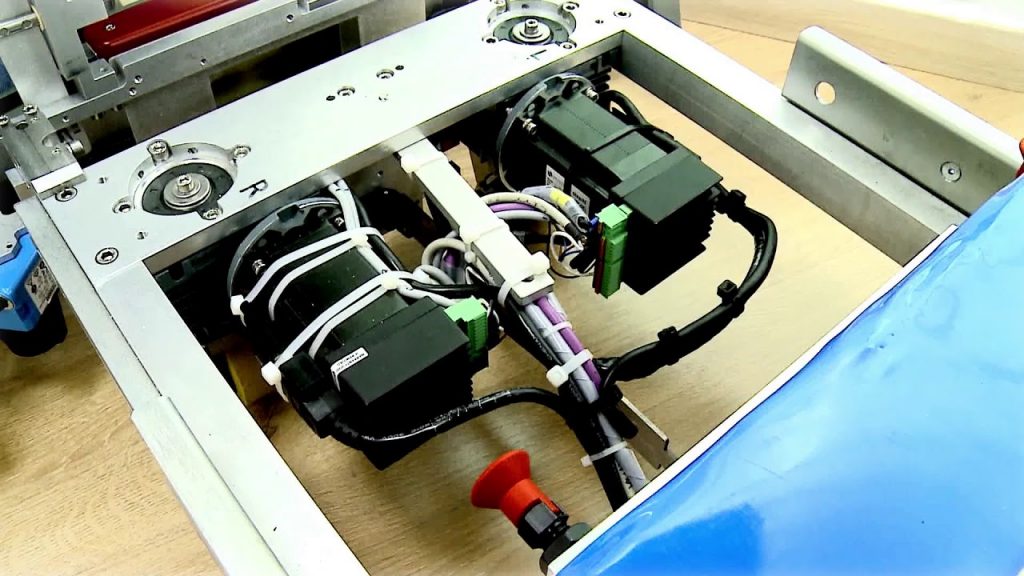
Source: servotronix.com
You cannot really choose the first encoder that comes in your search results, instead, you’ll have to consider the conditions around it. The things you need to consider include the following:
- The Motion Type + Speed – you should think about how the device will come in contact with other components that move and you must also know how fast that movement is.
- The Installation Location – will you install it on the motor or somewhere else? The installation location is important since different areas will require different devices.
- DAQ or DAS – the model you opt for will send signals to a DAQ system, hence, determine what input signals does your system requires and expect.
- Electricity Supply + The Length of The Cables – the device you purchase will need electricity to function, so, you should consider how many cables you’ll need.
- The Mechanical System + Design – you need to consider the mechanical system since the system accuracy will depend on your answer. Also, if you’re still designing your machine, you’ll have more device options.
The Motion is Important
The options you can choose from will depend on the motion in your system. Basically, you’ll have to option – a linear motion that happened in a straight line and rotary encoders that are most commonly used with components that rotate. No matter what option you choose, it can be used for calculating the distance, direction, as well as speed.
Magnetic, Optical, or Capacitive?
There is a wide range of options such as the ones featured on Encoder.com, which means that you’ll need to carefully consider what you should purchase. There are three main categories of these devices, including:
- Magnetic – as the name implies, it features a magnet that is installed on a rotating component. A sensor will detect the field lines from the magnet, which will then report the angle of the magnetic field. They can be used in moist and dusty environments and they usually consume less electricity.
- Optical – which are the most popular option out there and they usually feature a disk with transparent areas. It uses light to give you feedback information on the motion within your system and keep in mind, it cannot be used in moist and dirty areas since it might hinder the device from working.
- Capacitive – which is a tech that is relatively new. It functions by detecting any change in the system by utilizing a transmitter that sends out a high-frequency signal to a receiver. They also combine the two benefits of the aforementioned options, which means that they can work in dusty and moist areas and they consume less electricity.
Determine What Size You Require
These devices come in a wide range of sizes and things such as the housing and connector style will impact the overall size of the encoder. There are three options to choose from, with the first one being a large encoder. It’ll require durable housing, hence, it’ll be bigger than other options.
Next, you have the medium size, which means that the device will probably have dimensions that go from 1 to 3 inches, and, of course, there are the small models which are commonly used in electronics. This means that you could ever purchase an encoder that is smaller than 1 inch.
What Will Be The Speed of The Device

Source: heidenhain.com
Last on this list, but also important is to consider at what speed the device will be operating. Speed is an important consideration since it can affect the performance of the encoder. Generally speaking, all mechanical models will have a max speed, which can influence your decision when choosing between a model with bearings and one that has sleeve brushing.
On the other hand, for electrical models, the speed will influence the bandwidth of the entire system. The signals sent by the device you purchase might deteriorate at higher speeds, mostly because they’ll have less time to report the movements of the parts. So, ensure that you learn more about the speed you’ll need the device to feature.
Conclusion
To be completely honest, choosing an encoder for motion control applications is a daunting and time-consuming process, mostly because there are a lot of things you’ll need to consider. But, if you choose to follow some of the advice we mentioned above, you’ll make the entire process easier, but more importantly, you can ensure that you choose right.
So, now that you’re aware of all the things you need to consider, you shouldn’t waste any more of your time. Instead, you might want to return to the beginning of your list and start with the first thing we mentioned – which is determining whether or not you really need this device.