The casting process is well known to everyone. It includes several key stages such as melting the material, using the mold and shaping the finished part. However, the whole job is much more complicated, because it also contains a number of transitional phases. There are also a number of different metal casting processes. We must mention that there is a clear difference between them, which is why you should learn more about individual types. They all have several features in common. For example, each process involves melting a metal alloy, pouring the material into molds and shaping. In addition, we can list a few more features such as finishing, metal shrinkage, etc. If you want us to reveal all the main pouring techniques and useful information about them, keep reading.
1. Sand Casting
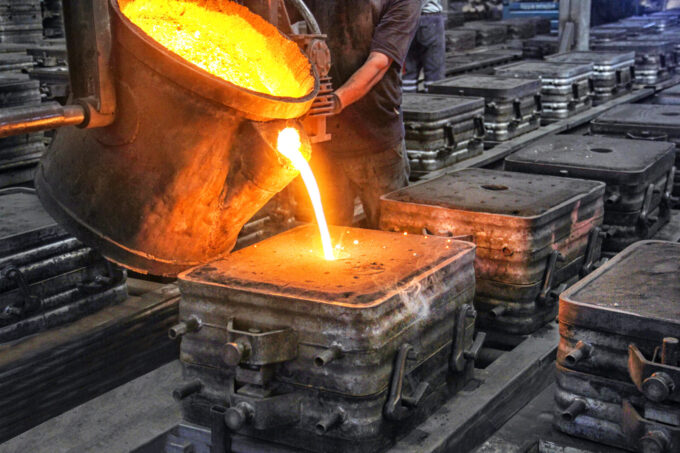
Source: weld2cast.com
This is definitely one of the most popular and simplest types of casting that has always been used. Silicon-based material is mainly used. The sand contains finely ground, spherical grains that pack perfectly together and form a smooth shaping surface. Sand casting is most often used for the purpose of producing large parts. It involves filling the molten metal into the cavity of a mold formed by sand. After the process was completed, a work item was obtained. If you want to get harder sand, use clay. It is used as an additive to help particles bind tightly. Sand casting involves several steps. First, a pattern is made, which can be a product of wood, metal or some other material, and it is made with various tools and equipment.
Then, the mold is prepared using templates and cores for making. This is followed by melting and casting. It is necessary to wait a while until the material hardens and only after that the cast part is removed from the sand. Finally, the casting is tested for various defects. The benefits of this process are numerous. Some of them are low price, large selection of sizes and a wide range of metals. It is especially suitable for making objects with complex internal cavities. Disadvantages are poor finishing and wide tolerance.
2. Investment Casting
It is a relatively simple casting process. It has been around for thousands of years and is known as one of the oldest metal forming techniques. The result of the process is product of high quality specifications that offer accuracy, repeatability, versatility. Another name for investment casting is the lost wax method. It involves the following few steps. The choice of material is made first. Selection comes down to easily soluble materials. Then, the surface is covered with several layers of refractory material and thus the shell of the casting part is obtained. It is mainly used for making ornaments and jewelry, but also for many other purposes.
The main advantages are a high degree of accuracy and precise dimensions. Thanks to this method, you can also get thin walls with complex geometry. You can also use broken materials. However, this casting choice is more expensive than some other techniques and is only cost effective if you cannot use sand or gypsum castings. There is a possibility of reimbursement if you reduce processing costs or save on tools.
3. Die Casting
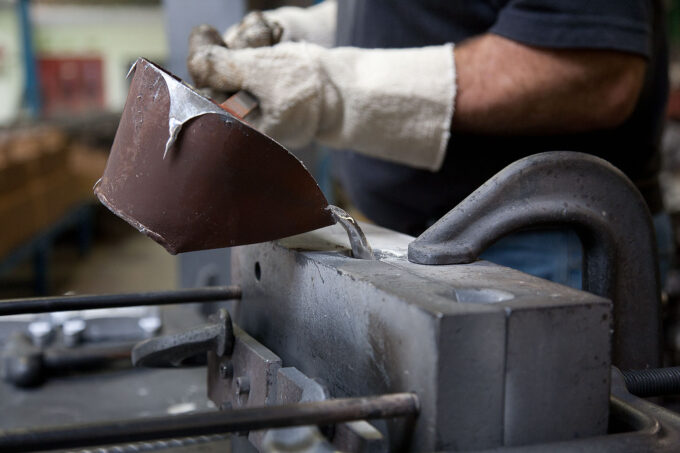
Source: squarespace-cdn.com
Die casting is used to form alloys of iron, aluminum, non-ferrous metals and the like. It is known for the use of a mold cavity for the purpose of applying high pressure to molten metal. Mold processing is done by machines and the whole process is reminiscent of injection molding. If you want to use this method, you need a cold chamber. You can also get a hot pressure die casting machine. Both types of machines contain the same main components and they are a source of molten metal, the same mechanism, mold and clamping system. A reusable mold is included in the process, which is coated with a lubricant when removing components. The molten metal is then injected into the mold under high pressure and this is done until the object hardens.
When the process is complete, the waste material is removed and the component is removed from the mold. It is mainly used for the purpose of making applications that require a lot of small and medium parts. Die casting will allow you to produce parts with good details, fine surface and a wide range of dimensions. The disadvantages of this method are expensive molds. Due to the relatively high cost of tools, the process is cost-effective only in large series of products. We must note that sometimes it can be difficult to provide the mechanical properties of the cast component. If you are interested in die casting, you can always learn more on specialized websites.
4. Low-pressure Casting Process
The process is very similar to sand casting. Thus, the metal melts after which it is filled into the mold by gravity. It lasts longer than high pressure casting, and involves the following steps. After the metal has melted, pressure is used to fill the mold with liquid metal. In the end, an outflow is formed, the metal hardens under pressure. One of the biggest advantages of this process is that you can influence the pressure and speed of pouring liquid metal. This means that you will get more accurate results and you can use different molds for casting. The whole process is very simple, fast and you will not have to turn on the gas. You will get a very clear outline and a smooth surface. You also need simple equipment that is used for mechanization and automation.
5. Centrifugal Casting Process
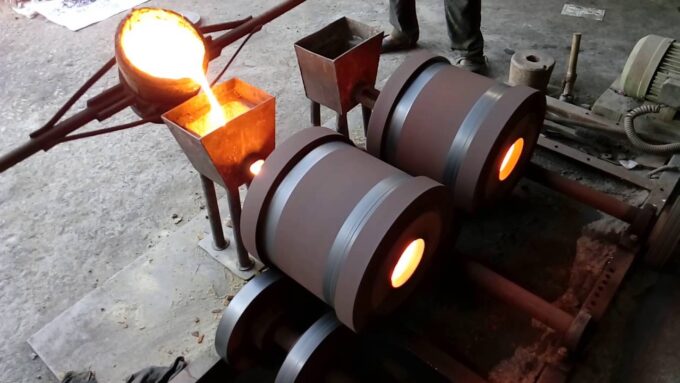
Source: youtube.com
In this process, it is necessary to pour the molten metal into a rotating mold that is under the action of centrifugal force. This will strengthen and form the shape. It is mainly used to make axi-symmetric parts that are hollow. Centrifugal pouring has almost no drawbacks, and is a great option for cast pipes.
Conclusion:
Compared to all other production processes, casting has many advantages. Thanks to this process, you can create any complex structure. You can also choose any size you want, because there are no restrictions in that regard. Casting items are extremely resistant to pressure. The molds are created so that you can create the object you want. You can cast any material at a very reasonable price.