If you’re looking for a simple and cost-effective way to connect the terminals of a flat or ribbon cable, you might just find an IDC connector to be the best choice. Short for insulation-displacement contact, these are usually incredibly easy to use and often well worth looking into.
If you’re hoping to use some IDC connectors, you might be a little overwhelmed by the variety of options. From a locking clamp vs cable clamp, 2 pins or 40, there are certainly quite a few to choose from.
What are IDC connectors used for?
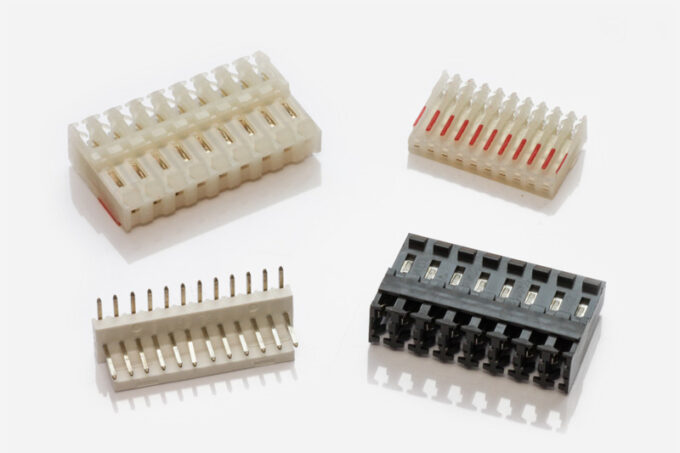
Source: fclane.com
Created to make the mass termination of cables easy, it’s not hard to see why so many people use these types of connectors. The idea behind it is simple; the connector contact is sharp enough to pierce through the wire’s insulation, so you won’t need to strip the insulation yourself. These are very common for ribbon cables, as well as flat cables.
If you’re interested in seeing what’s on offer, be sure to take a look at some of the different connectors that are available on https://www.tme.com/us/en-us/katalog/idc-connectors_112943/.
What do you need from an IDC connector?
There are quite a few ways that insulation-displacement contact connectors can vary – allowing you to find the ideal ones for your unique needs. Of course, the type of connector that works best for you will often rely mostly on what it is you need to use it for, so keep this in mind while shopping.
Consider factors like the number of pins, type of connector, and the cable that needs to be terminated. In general, the best way to make the right choice is to simply know what it is that you require for your project. On the plus side, it isn’t usually too much of a tough task to purchase the connectors that are right for you.
Choosing the right brand
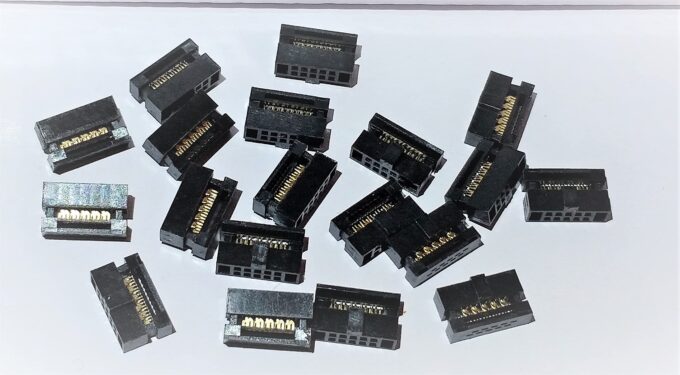
Source: amazon.com
You’ll also find that there are plenty of brands available, which might add another layer of complication to making your decision if you’re already unsure about what to buy. In general, one of the best things you can do is consider your options and make sure that the manufacturer you’re buying from is reliable. From CONEC, to Amphenol ICC; be sure to take the time to find a reputable company to get your connectors from.
To make the end product more durable and water resistant, many companies encapsulate their products with a final coat that helps protect it from dirt or other elements. This process can affect how well your electrical connections function though so be sure you know what kind of warranty coverage comes standard before buying!
With so many options for connectors on the market, it’s hard to sift through all of their technical attributes and choose which one will work best in your application. The IoT has caused an exponential increase demand in this area that resulted into more smart products being created with expanded connectivity capabilities- making everything from washing machines down south (I bet you didn’t know they had personalities!)to elevators up north alive!
The ability to survive in harsh environments is something that modern connectors have mastered. As such, they can be found on outdoor products like mobile phones and transportation devices with increasing frequency due their capability for reliably transferring data no matter what condition it faces off against
When it comes to end products for harsh outdoor, mobile and transportation applications there’s a common theme: potting or overmolding. This final encapsulation process can negatively affect the electrical and mechanical integrity of connections on most PCBs because they are often soldered directly onto boards rather than being plugged in like connectors which make these treatments less effective (but not always).
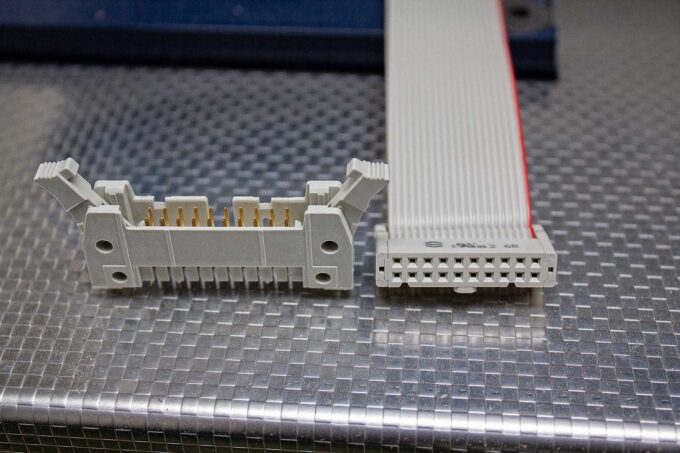
Source: harting.com
Connectors are special because they function under the principle of applying and maintaining compression force between two surfaces to make an electrical connection. For example, a connector with good conductivity will survive severe temperatures without issue; however if we add in foreign materials like PVC or rubber then our concern for RI grows stronger as these cannot withstand such high levels…
The potting and overmolding materials can leech into the contact area, insulate against heat or cold causing an immediate electrical failure. These failures may be worse yet because they prevent contacts from maintaining sufficient force for long periods of time resulting in unanticipated field failures later down road
The solution to this problem is surprisingly easy; all we have do it solder the wires onto our PCB like every other component. However, unlike with SMT processes where everything else goes through an automated process and gets checked for perfection (including Soldering), there are many variations in manual soldering which makes it time consuming AND costly!
IDC connections are a reliable solution to the problems that often arise when potting or overmolding connectors for harsh environment applications. It has roots dating back more than 50 years and continues evolving into one of most trusted contact technologies employed in automotive as well other transportation sectors, but there’s always room for improvement with current designs because they can’t withstand radiation exposure from storage media like computer monitors which might cause short circuits if left unchecked by dust particles constantly scrambling their way through your hardware store shelves.When it comes to connecting wires, you need a strong bond that will last. A cold-welded metal on metal connection is what’s required for this level of protection and can only happen with an IDC connector. The size difference between AWG wire and contact slots means there has always been some risk involved when creating these types connections; however through careful design work by engineers like themselves – who know how important their job really is! With the introduction of this new design, IDC technology has been able to overcome what was once considered a significant barrier in terms on delivering power sources for demanding applications. The original conception behind it all centered around insulated stranded-wire use cases but over time evolved into accommodate solid wire and single conductor constructions as well.