Processing plastic materials is a complex process that involves several stages, starting from the raw material and ending with the finished product. There are three types of plastic material processing: hot processing, cold processing, and mixed processing. Today, we will focus primarily on hot processing. The process generally starts with the preparation of the material, which can be in the form of pellets or powder. The material is then fed into a specialized processing machine, where it is melted at high temperatures and then molded into the desired shape.
There are different methods of processing plastic materials, including:
- Extrusion: using an extruder, which is a screw machine that melts the material and pushes it through a die to create a continuous profile. Extrusion is used to create tubes, profiles, films, and other similar products.
- Injection molding: injecting melted material into a mold where it solidifies and takes on the desired shape. Injection molding is used to create solid plastic objects, such as containers, covers, and other similar products.
- Blow molding: using preheated preforms that are blown into the desired shape. Blow molding is used to create plastic containers, such as bottles and jars.
- Thermoforming: heating a plastic sheet and shaping it while it is hot. Thermoforming is used to create plastic objects such as trays, blisters, and other similar products.
These are the most commonly used plastic material processing techniques, but there are also other less common methods such as compression molding, rotational molding, and lamination.
Regardless of the chosen method, plastic material processing always requires careful selection of raw materials and accurate control of temperature and pressure, in addition to the use of specific equipment, to ensure quality.
Let’s go into more detail, trying to answer some of the most frequently asked questions about these processing methods.
What is the plastic material granulation process?
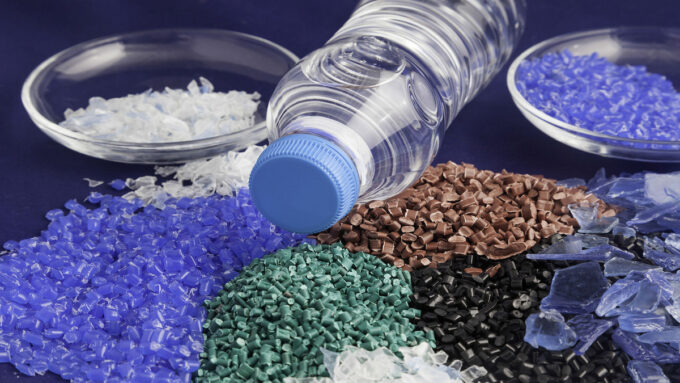
Source: youtube.com
Plastic material granulation is an industrial process used to transform plastic material into granules, which are subsequently used in various industrial sectors.
The granulation process generally develops in the following order:
- Preparation of the material.
- Drying.
- Granulation (the material is fed into a granulating machine where it is compressed, heated, and then extruded to form filaments, which are then cut into granules with a rotating blade. The size of the granules can be controlled according to customer needs).
- Cooling.
- Screening, to remove any impurities or non-granular parts.
- Packaging.
The plastic material granulation process is an important operation for the production of high-quality plastic products. The choice of the right granulation technology and the monitoring of its processing parameters are crucial to ensure the quality of the produced granules and their success in the production of plastic products.
Why is drying and dehydration of plastic pellets important?
Drying and dehydration of plastic pellets are important because they ensure that the material is free from moisture.
The presence of moisture inside plastic material can cause several problems during processing and production, such as:
- Product quality issues due to bubbles and/or spots on the surface.
- Processing problems, affecting the viscosity of the material and altering the flow and adhesion.
- Safety issues, related to the formation of toxic gases during processing.
- That’s why drying and dehydration of plastic pellets are essential to ensure the quality and safety of your work and the product you offer.
Why is material transport relevant for plastic processing?
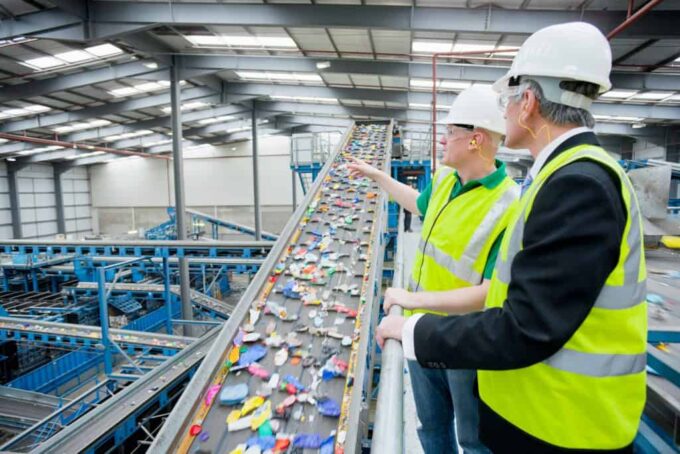
Source: youtube.com
Material transport is a crucial aspect of plastic processing because it affects the quality of the final product.
Thanks to it, it’s possible to avoid contaminations, preserve the properties of the material, prevent damages, and ensure uniform processing.
Material transport systems for material handling in the plastic industry can be hydraulic, mechanical, or pneumatic, depending on specific needs.
Transporting material from point A to point B (more precisely from the storage location to the processing machine) may seem like a relatively simple activity, but it’s not!
The increase in automation and shorter cycle times has made Vismec technological evolution indispensable even in this aspect.
Today, plastic processing machines are predominantly equipped with vacuum material loaders, but how is plastic pellet separated from the transport air?
Let’s answer this too…
How is plastic pellet separated from the transport air?
Plastic pellet is separated from the transport air through a filtering system.
The transport air is pushed through a filter that retains any dust or impurities, while the plastic pellet passes through the filter and continues along the transport system.
The filter used to separate plastic pellets from transport air is usually made of a porous material, such as filter paper or a wire mesh.
Less frequently, a centrifugation system is used to separate the pellets from the air, thanks to the centrifugal force generated by the rotation of the transport system.
Separating plastic pellets from transport air is crucial to ensure that the material arrives at its destination without contamination, which could compromise the quality of the finished product.
There would still be many questions to answer, but with this article, we’ve covered the main essential aspects of plastic material processing, even on specific and technical aspects.
Microplastic solutions for medical usage: Pharmaceutics and Cosmetics
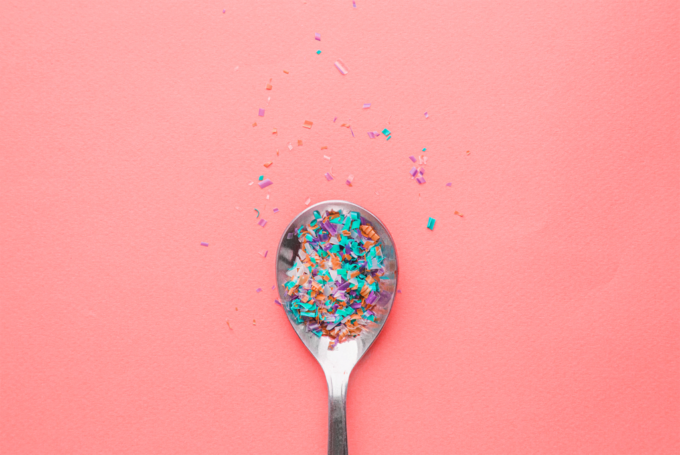
Source: pinterest.com
Microplastic solutions are important also for medical usage.
But in pharmaceutics and cosmetics have been a topic of debate in recent years.
In the medical field, microplastics have been used as drug delivery systems, where drugs are loaded onto the surface of the particles and then delivered to targeted cells in the body. This can improve the efficiency and effectiveness of drug delivery, as well as reduce the side effects associated with traditional drug delivery methods.
However, the use of microplastics in cosmetics has raised concerns about the potential environmental impact of the products, as microplastics can be difficult to remove from water systems and can end up in the food chain.
Some countries have already banned the use of microplastics in certain cosmetic products.
Overall, the use of microplastics in medical and cosmetic applications requires careful consideration of the potential benefits and risks, as well as the environmental impact of the products.