Stainless steel manways, integral components in tank systems, are crucial in various industries for providing secure and reliable access. These manways, typically made from high-grade stainless steel, offer robustness and resistance to corrosion, making them ideal for tanks used in a wide range of applications.
Their importance lies not just in providing access for maintenance and inspection but also in ensuring the safety and integrity of the storage systems. These manways are a testament to the innovation in material engineering, catering to the demanding environments of industries such as pharmaceuticals, food processing, and chemicals.
The Role of Manways in Tank Systems
Manways are essential for the functionality and safety of tank systems, serving as access points for personnel to perform crucial tasks like inspection, maintenance, and cleaning. These openings must be designed with safety and efficiency in mind, ensuring they are robust, leak-proof, and easy to operate. This is particularly vital in industries dealing with hazardous materials or high-pressure environments.
The role of manways extends beyond access; they play a critical part in maintaining the structural integrity and operational efficiency of tanks. Properly designed manways contribute to the overall safety and longevity of tank systems, making them a key focus in tank design and construction.
Industrial Applications of Stainless Steel Manways
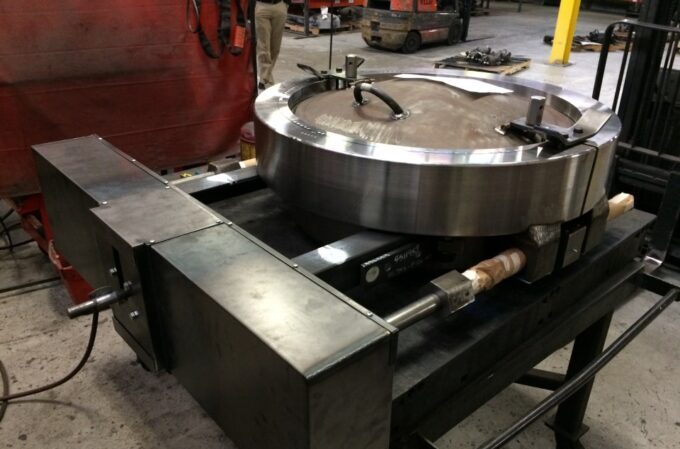
Source: linkedin.com
Stainless steel manways such as those from Inoxmanways find their applications in a myriad of industries due to their superior durability and corrosion resistance. In the food and beverage sector, they are essential for maintaining hygiene and preventing contamination. Pharmaceutical industries rely on them for their inert nature, ensuring no chemical reactions with stored substances. Chemical processing industries appreciate their resistance to corrosive substances.
Even in sectors like wastewater treatment and petrochemicals, stainless steel manways are preferred for their long-term reliability and strength, accommodating various environmental conditions and operational demands. Each industry’s specific requirements dictate the customization and design of these manways, showcasing their versatility and importance in modern industrial applications.
Types of Stainless Steel Manways
There are various types of stainless steel manways, each designed to meet specific needs and tank configurations. These include circular, oval, and rectangular manways, each offering different advantages in terms of accessibility and space utilization.
The selection often depends on factors like the size of the tank, the nature of the stored substance, and the environmental conditions. Pressure-rated manways are used in tanks holding gases or liquids at high pressure, while non-pressure types are common in storage and fermentation tanks. For fermentation applications, you could use stainless steel manways with glass lids for easy viewing. Specialized designs like hygienic manways are crucial in the food and pharmaceutical industries, where cleanliness and contamination prevention are paramount.
Key Features of Stainless Steel Manways
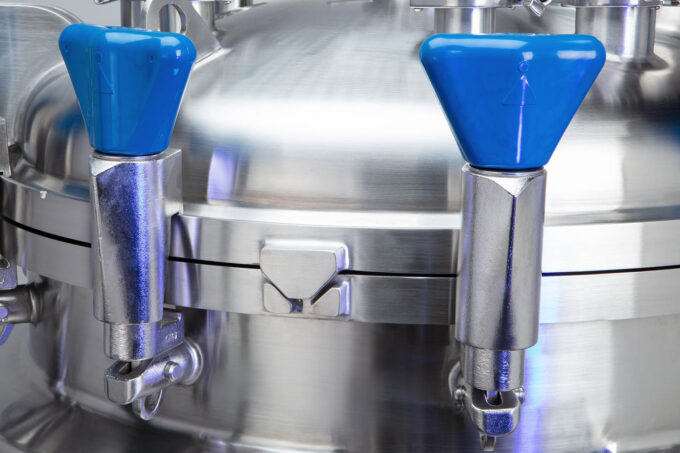
Source: hollowayamerica.com
Stainless steel manways are chosen for their distinctive features like corrosion resistance, durability, and hygiene. Their construction from high-grade stainless steel makes them resistant to a wide range of chemicals, ensuring longevity and reliability in harsh environments.
The smooth, non-porous surface of stainless steel is ideal for maintaining hygiene, especially in industries like food processing and pharmaceuticals. Furthermore, the strength of stainless steel allows these manways to withstand high pressures and temperatures, making them suitable for a variety of industrial applications. Their design also includes features like quick-opening mechanisms and secure sealing options, enhancing their functionality and safety.
Benefits of Stainless Steel Manways
Using stainless steel manways offers numerous advantages over other materials. Their corrosion resistance translates to a longer lifespan, reducing the need for frequent replacements and maintenance. This long-term reliability is a cost-effective solution for industries looking to minimize downtime and maintenance costs.
Stainless steel manways are also known for their hygiene and cleanliness, crucial in industries where contamination is a concern. Their ability to withstand extreme conditions makes them versatile for various applications, ensuring operational efficiency and safety.
Efficiency Tips for Installing Manways
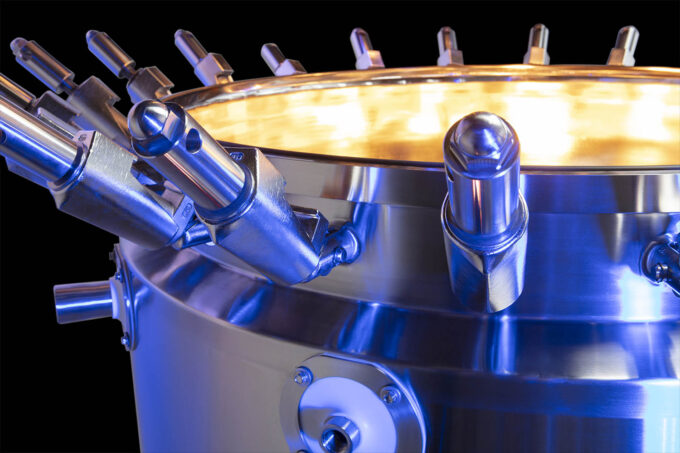
Source: hollowayamerica.com
Efficient installation of stainless steel manways is key to maximizing their benefits. It is crucial to ensure proper alignment and sealing to prevent leaks and maintain tank integrity. Regular maintenance, including checks for corrosion and damage, extends their lifespan.
It’s also important to follow safety protocols during installation and maintenance, especially in environments with hazardous materials or high-pressure tanks. Adequate training for personnel handling these installations is essential for ensuring safety and efficiency.
Choosing the Right Manway for Your Application
Selecting the most suitable manway for a specific application involves considering several factors. The nature of the tank contents, whether liquid, gas, or solid, plays a significant role in the choice of manway. The size and pressure rating are other critical considerations, as they must match the tank’s specifications.
Additional features like quick-opening mechanisms or special seals might be necessary depending on the industry and specific operational requirements. Understanding these factors ensures the right manway is chosen for optimal performance and safety.
Maintenance and Inspection Procedures
Regular maintenance and inspection are vital for the longevity and safety of stainless steel manways. A systematic approach, including routine checks for signs of wear, corrosion, and seal integrity, is essential. A step-by-step inspection process should be established, covering all aspects of the manway, from the hinges and bolts to the sealing surfaces.
Addressing common issues promptly, like replacing worn gaskets or tightening loose components, helps maintain the manway’s functionality and safety. Proper documentation of inspections and maintenance activities is also crucial for compliance and operational records.
Case Studies: Successful Manway Applications
Real-world examples highlight the impact of stainless steel manways across industries. In a brewery, the installation of hygienic stainless steel manways significantly improved the cleaning process and reduced contamination risks.
In the chemical industry, custom-designed pressure-rated manways enhanced safety in high-pressure environments. These case studies demonstrate the versatility and efficiency improvements that stainless steel manways bring to different operational contexts, showcasing their contribution to safer and more efficient industrial processes.
Regulatory Compliance and Safety Standards
Adherence to regulatory requirements and safety standards is crucial in the use of manways. Standards vary by industry and region, covering aspects like material specifications, design pressure ratings, and safety features.
Compliance ensures not only the safe operation of the tanks but also the protection of workers and the environment. Regular audits and updates on regulations are necessary to keep up with evolving standards and technological advancements.
Conclusion and Future Trends
Stainless steel manways for tanks are vital components in various industries, offering durability, safety, and efficiency. They have evolved to meet the diverse requirements of different sectors, with ongoing innovations in design and materials.
Future trends may include the integration of smart technologies for monitoring and maintenance, further enhancing their functionality. The continuous development in manway technology promises to bring more efficient and safer solutions to the industrial world.